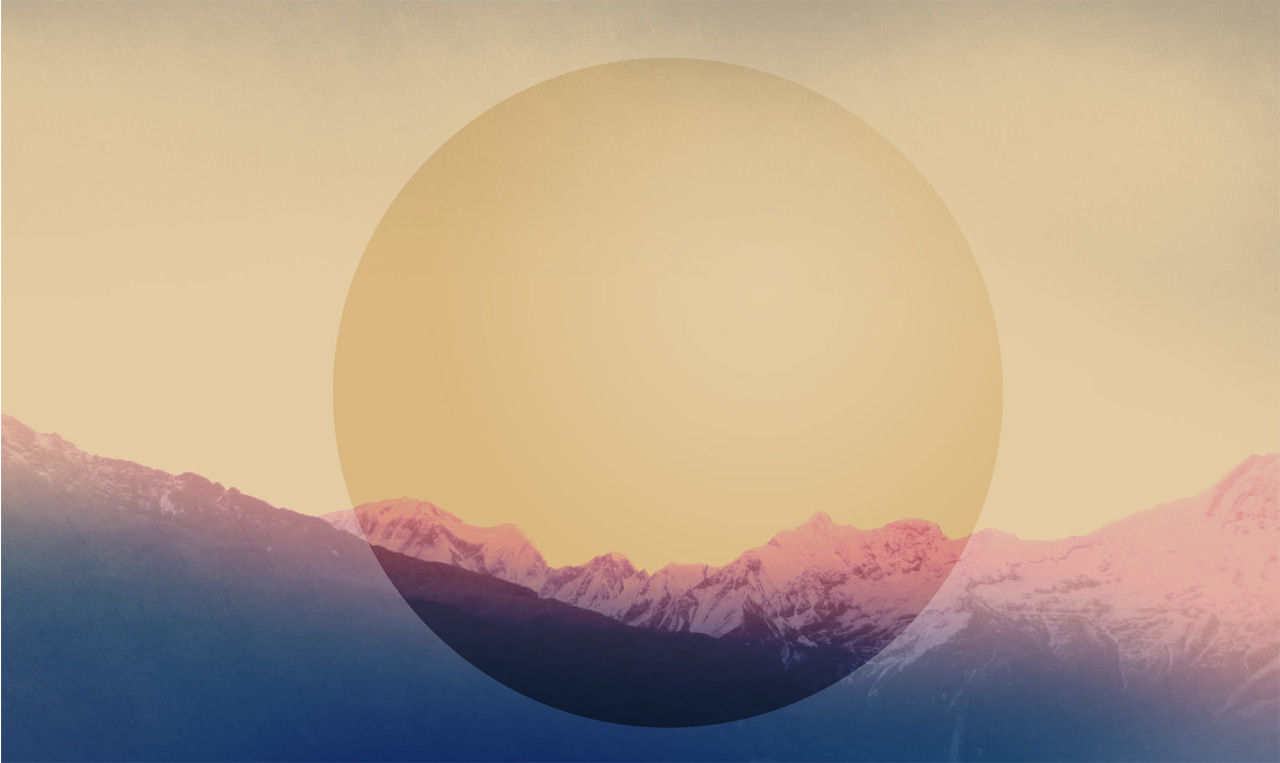
Seguici anche su:
Tecnologie Ambientali
Trattamenti termici
I trattamenti di tipo termico sono quelli più efficienti in termini di riduzione di volume e di peso, e gli unici che permettono un discreto recupero di energia e, in alcuni casi, addirittura uno sviluppo di energia tale da ripagare, alla lunga, l’ investimento iniziale.
Distinguiamo in base al processo questi 3 metodi:
-
Incenerimento
-
Pirogassificazione
-
Atomizzazione tramite plasma
Quando queste tecnologie vengono utilizzate non solo per smaltire materia ma anche per produrre energia che non sia di solo recupero vengono chiamate in ambito internazionale WTE, ossia Waste To Energy. Esaminiamole distintamente.
Incenerimento
L’ incenerimento, attualmente chiamato in genere termovalorizzazione in quanto la normativa italiana ormai autorizza l’ incenerimento solo per recupero energetico, è la più vecchia tecnologia di trattamento termico dei rifiuti. Storicamente l’ incenerimento si è basato su diversi processi, alcuni molto semplici seppur molto efficienti relativamente al compito che dovevano svolgere, i quali però sono sempre stati osteggiati dalla popolazione e, in modo particolare, dai ‘rinnovabilisti’, cioè tutti quegli ambientalisti dell’ ondata post-decreto Ronchi (1996) i quali spesso in malafede denigravano la tecnologia dell’ incenerimento a causa di limitati casi in cui alcuni impianti si son dimostrati fortemente inquinanti.
Le modalità principali di incenerimento si basano in sostanza su tre processi o tecniche:
-
Griglia mobile
-
Tamburo rotante
-
Letto fluido
La tecnica a griglia mobile utilizza una camera a combustione nella quale una griglia supporta i rifiuti caricati tramite un braccio meccanico o carro-ponte / gru. Questa griglia si muove in percorsi regolari (nel senso di automatizzati) o irregolari (nel senso di hand-pilot, diretti da sala controllo da un quadrista) in modo da uniformare l’ effetto dell’ incenerimento ed avere una maggiore e migliore esposizione del solido alle fiamme. Nella maggioranza dei casi il percorso è fisso e realizzato su almeno 3 livelli, realizzando così una sorta di percorso a ‘scala’.
La tecnica a tamburo rotante utilizza un vessel cilindrico generalmente disposto in posizione obliqua angolata tra 1 5 e i 15° e ‘disassata’ rispetto alla diagonale del flusso in modo che al suo interno i rifiuti vengano fatti ‘rotolare’ e vengano smossi continuamente mentre esposti al calore. Questo può essere diretto (sistemando degli ugelli di fiamma nel cilindro) o indiretto (esponendo le pareti del cilindro alla fiamma) anche se la grande maggioranza dei casi reali utilizza il fuoco diretto. La temperatura di processo si aggira generalmente tra i 1000 e i 1200°C. Alla base del cilindro si accumulano i solidi incombusti e le ceneri della combustione, mentre dall’ alto vengono estratti i fumi che vengono diretti in una seconda camera di combustione. L’ alta temperatura raggiunta causa normalmente una elevata produzione di impurità a base di zolfo, azoto, e micro polveri, rendendo obbligatorio un sistema di filtrazione e trattamento dei fumi.
Nella tecnica del letto fluido si utilizza una fornace verticale riempita sul fondo da sabbia alla quale possono essere mischiati additivi o sostanze capaci di catturare particolari inquinanti (es: la dolomite e il carbonato di calcio per catturare lo zolfo). Sotto questa sabbia viene insufflata aria calda in pressione, la quale fa innalzare il letto di sabbia e lo tiene in continuo movimento; in questo sistema, tramite dei condotti laterali a caduta, vengono introdotti sia i rifiuti che il combustibile, i quali vengono a mischiarsi con il letto di sabbia e aria calda. Il sistema così realizzato svolge varie funzioni contemporaneamente: le sabbie erodono alcune parti dei rifiuti, gli additivi catturano le componenti chimiche quali lo zolfo e ne riducono il tenore nei fumi, il sistema diventa semi-fluido e ne viene ridotta sensibilmente la densità .
Una delle caratteristiche principali di questo tipo di camera a combustione è che permette temperature più basse rispetto agli altri metodi, generalmente sotto i 900°C, minimizzando quindi la formazione di particelle azotate (NOx). Inoltre la tecnica a letto fluido si rivela più efficiente nella riduzione a ceneri dei rifiuti, fino a 4 volte rispetto alla classica griglia mobile.
Il grado di efficienza riscontrabile in queste tecniche è di questo ordine:
letto fluido > tamburo rotante > griglia mobile
Le tecnologie di incenerimento hanno una buona resa sia in termini di riduzione di peso che di volume, generando un residuo tra il 5% e il 15% in peso del totale caricato e con una riduzione di volume che varia tra il 15:1 e il 20:1.
Pirogassificazione
La pirogassificazione è un processo molto complesso nel quale si possono individuare 3 fasi: una essicazione (o evaporazione), una pirolisi termica (rottura termica dei legami) e una gassificazione (una combustione in carenza d’ aria). Questa tecnologia può essere utilizzata per ogni genere di rifiuto solido a base organica, anche ad altissima umidità (35-50%, minore è l’ umidità maggiore è il rendimento), ma trova la sua principale applicazione nello smaltimento delle biomasse umide. Il risultato del processo di pirogassificazione è triplice: da un lato otteniamo un gas pulito composto principalmente di idrogeno e di monossido di carbonio (chiamato syngas, utilissimo per produrre energia), dall’ altro il residuo solido (minimo) è una sorta di carbone catramoso (chiamato Char) anch’ esso riutilizzabile e il residuo liquido (chiamato Tar o ‘olio di pirolisi’) è molto utile in ambito energetico o come biocombustibile.
La tecnologia di pirogassificazione (o piroscissione) si avvale di speciali caldaie che lavorano intorno ai 700-800°C, anche se particolari processi specifici (come il Thermofuel) permettono di abbassare la temperatura fino anche a 400°C.
La gassificazione che avviene dopo la piroscissione non può essere inquadrata propriamente in una combustione, in quanto avviene in rapporto sub-stecchiometrico ossigeno/combustibile, producendo reazioni non completamente ossigenate. L’ ambiente di gassificazione è generalmente inertizzato con azoto.
Atomizzazione al Plasma
La tecnologia basata sul plasma sfrutta due tipi di iniezione: l’ arco elettrico o la fiamma. Il tipo di iniezione è scelto in genere in base al tipo di carica da alimentare (uno stream voluminoso e di forma/superficie irregolare è meglio gestibile con una iniezione a fiamma) e al sistema di controllo della ‘camera’ che si vuole implementare (un arco elettrico ci libera dall’ obbligo di controllare il sistema di iniezione in quanto non abbiamo problemi di ritorno di fiamma, depositi di combustione etc.). Il principio di funzionamento comunque è lo stesso: si produce una iniezione energetica in uno spazio confinato in cui viene fatto passare un mezzo fluido il quale viene portato a temperatura altissima (tra 6000 e 9000°C) ottenendo così un ‘plasma’ di calore che viene trasportato poi sulla superficie da ‘atomizzare’ tramite una corrente di gas. Alternativamente si può direttamente coinvolgere il solido da distruggere nello stream di fluido ignito. Al centro della fiamma e nelle sue immediate vicinanze, la temperatura causa un’ atomizzazione presso chè istantanea di ciò con cui viene a trovarsi in contatto; al crescere della distanza dalla fiamma la temperatura diminuisce, fino a generare un ambiente medio intorno ai 3500-4000°C (nei processi ad altissima temperatura) o ai 2000-3300°C (nei casi di processi ad alta temperatura). A queste temperature di ambiente i materiali non bruciano, né gassificano: vengono atomizzati, cioè distrutti nelle loro componenti fondamentali. Con questo metodo non si può più parlare di ‘composti’ ma di elementi, dunque va da se che non esistono più composti nocivi quali NOx, SOx, PCB, diossine, furani etc. Esistono solo azoto, zolfo, idrogeno, ossigeno, carbonio etc. Tutte le componenti organiche della carica subiscono questo processo di atomizzazione, vengono catturate, e portate via dall’ ambiente per generare gas energetico; le componenti non organiche e principalmente tutta la parte vetrosa, minerale e metallica, vengono fuse in una pasta inerte e non nociva, ad altissima densità e resistentissima (grado di durezza scala di Mohs: 5-6; resistenza a pressioni di 1100kg/mm2, riutilizzabile in tantissimi ambiti (edilizia, fonderia etc.). L’ efficienza della tecnologia al plasma è irraggiungibile da altre tecnologie: ha una riduzione di volume fino a 52:1 (la media si attesta intorno ai 45:1) e di massa fino a 30:1 (la media si attesta intorno al 23:1) e ha punte di conversione energetica dell’ 85-88%. Inoltre un impianto medio-piccolo necessita circa di un 22-25% dell' energia prodotta per alimentarsi, a fronte di un 30% circa per un impianto di taglia grossa. L' energia ricavabile da un impianto al plasma, allo stato attuale, può arrivare anche a valori di densità di 100-120 MW/m3.
Per approfondire il tema del metodo basato sul plasma consultare i seguenti articoli:
- scorie radiattive? C' é il plasma



