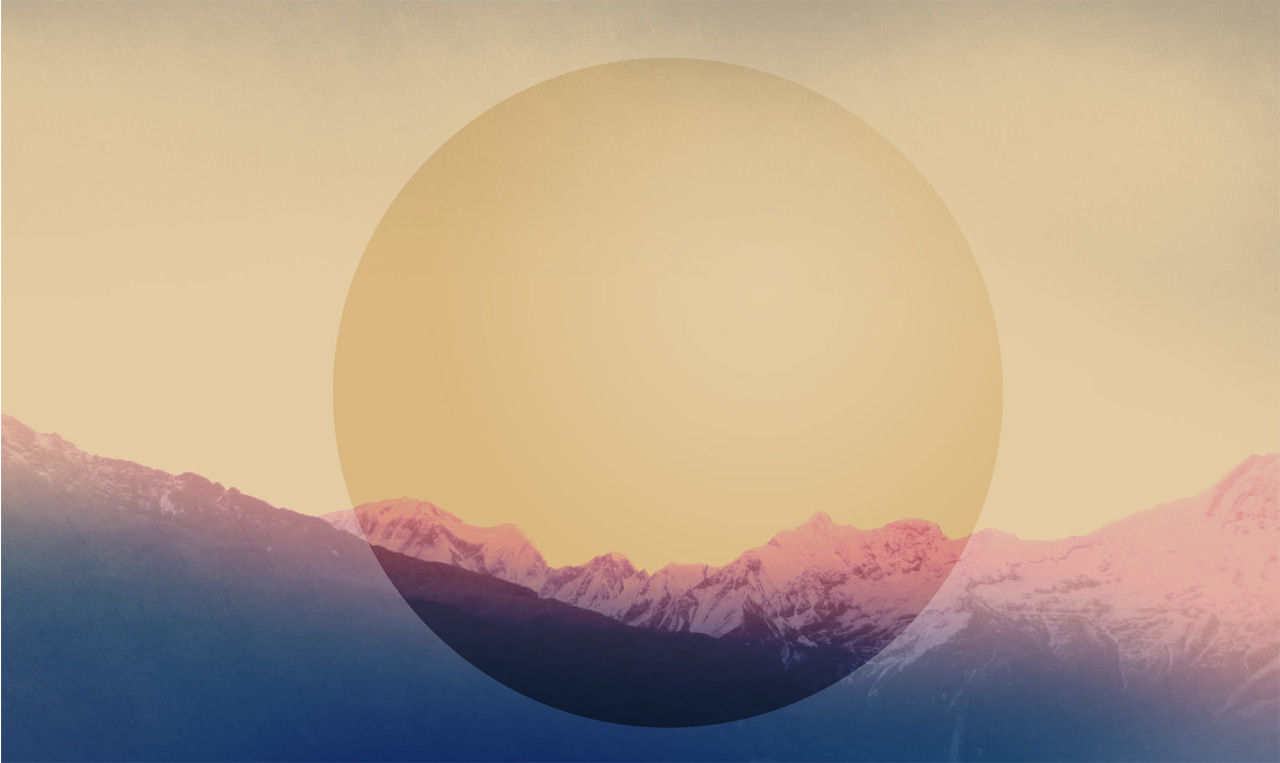
Seguici anche su:
Tecnologie Ambientali
Trattamenti meccanici di rifiuti
Tritovagliatura
Il termine Tritovagliatura racchiude in realtà due processi: la triturazione e la vagliatura, cioè la separazione delle varie componenti in base a principi scelti a seconda del processo che seguirà . Di solito la scelta é fatta tra materiali pesanti (ferro, plastica dura, vetro, etc) e materiali leggeri (carta e cartone, plastiche leggere, scaglie di legno etc). La vagliatura viene di solito prima della triturazione, specialmente in quegli impianti di rattamento meccanico che dedicano diversi strumenti alle diverse frazioni. La vagliatura può essere sia automatizzata sia manuale: uno dei metodi automatizzati più utilizzati é quello gravimetrico, in base al quale le varie frazioni sono separate in base alla loro capacità di penetrazione / galleggiamento in un mezzo fluido. Con questo metodo per esempio avremo una prima scrematura tra carta, cartone, chips di polistirolo, pet, scaglie di legno e altri metariali (anche metallici, quali l' alluminio) che non affondando in acqua da una parte, e plastiche pesanti, vetro, metalli ferrosi, e minerali che affondano in acqua dall' altra. Seguirà ulteriore separazione per esempio per eliminare alluminio e plastica dalla componente galleggiante.
La triturazione avviene (o meglio, può avvenire) sia prima che dopo il trattamento vero e proprio; la tritovagliatura in effetti é un pre-trattamento, cioè una operazione atta a preparare il carico rifiuti alle vere e proprie metodiche di trattamento. La tritovagliatura può essere applicata a tutte le frazioni, da quelle morbide a quelle più dure, semplicemente utilizzando lame e grate di triturazione di diverso materiale o forma.
Con la tritovagliatura si ha una riduzione in ordine di volume del carico rifiuti , ma se utilizzata da sola essa non permette una riduzione in ordine di peso.
L' immagine qui sotto mostra la sezione di un trituratore del tipo Pyromex:
Estrusione
Il processo di estrusione si applica alle plastiche, ad alcuni metalli, e a volte anche al vetro o più propriamente alla pasta di vetro. L' estrusione é un processo che agisce sulla forma, non implica una riduzione né in ordine di volume totale (salvo nel caso di estrusione a freddo di vetro, trattamento che però consiste più in una frantumazione) né di peso, ma permette di ottenere barre o chips di materiale da destinare a nuova produzione o lavorazione.
L' estrusione avviene in macchine chiamate estrusori composti da un imbuto di carico convogliante, una coclea o vite di estrusione, e una filiera, che in sostanza é una paratia contenente un ugello sagomato (a seconda delle forme che si vogliono dare alle barre). Gli estrusori devono essere alimentati con una notevole quantità di energia per trattare materiali duri specialmente metallici; l' estrusione delle plastiche può avvenire sia a freddo che a caldo, mentre quella del vetro avviene quasi esclusivamente a caldo successivamente alla produzione della 'pasta di vetro' tramite fonderia. Il trattamento di estrusione a freddo del vetro produce sabbia vetrosa anzi che barre, un processo quasi sempre evitato per l' alto potere penetrante delle sabbie di vetro nell' apparato respiratorio. L' estrusione a freddo delle plastiche si può applicare solo su gomme morbide, le quali vengono introdotte in chips nella coclea ed é il calore sviluppato dall' attrito a scaldarle e renderle più atte al passaggio nella filiera.
Qui sotto la sezione di un estrusore a caldo per materie plastiche:
Compattamento
Come la tritovagliatura, anche il compattamento é meramente un pre-trattamento, che serve a ridurre il volume dei rifiuti. Avviene in machine chiamate pelletizzatrici o imballatrici a seconda che debbano produrre pellets (chips o cilindretti di materiale) o balle.
Si tratta in sostanza di processi di pressatura ove occasionalmente (presse pelletizzatrici) interviene un processo di estrusione. Il compattamento é un' ottimo metodo per aumentare anche di molto i tempi di stoccaggio quando questo si renda necessario (pensiamo per esempio ai casi in cui gli impianti di vero e proprio trattamento siao in shutdown di emergenza o manutenzione, e i rifiuti continuano ad accumularsi... una buona compattazione permette di avere giorni e giorni di autonomia prima di arrivare a un punto critico)
Qui sotto una pressa imballatrice in azione:
Omogeneizzazione, strippaggio ed essicamento (per rifiuti liquidi o ad alto contenuto di umidità )
Per il trattamento dei liquami (acquosi ed oleosi che siano) i trattamenti meccanici si limitano a una omogeneizzazione (o al contrario filtrazione quando le due fasi non possono essere trattate contemporaneamente) e a successivo strippaggio ed essicamento. L' omogeneizzazione avviene in vasconi a larga sezione orizzontale e generalmente di altezza limitata; nei vasconi sono presenti una o più viti bracciate a pale o griglie che si muovono lentamente ma continuamente in modo da creare moti uniformi alle varie altezze mescolando così ed omogeneizzando i contenuti acquosi. Questa operazione é essenziale quando dovrà seguire un processo chimico (quale per esempio la chiaro-flocculazione) il cui risultato deve essere garantito su tutto il liquame evitando zone di inefficienza.
Qui sotto una vasca di omogeneizzazione:
Lo strippaggio é un processo che serve ad eliminare gas disciolti nella fase liquida. Pensiamo alle acque frizzanti, o a rifiuti liquidi nei quali rimanga disciolto del gas di fermentazione. Il processo può avvenire per differenza di pressione (colonne di vacuum fisico), per riscaldamento, o con l' utilizzo di entrambi i metodi (es: nello strippaggio del greggio, chiamato Topping, seguito da una fase di Vacuum, cioè di 'messa a vuoto' della colonna, che aspira verso l' alto i gas separandoli dal liquido.
Qui di seguito lo schema di processo di un sistema di strippaggio di acque acide:
L’ essicamento, o essicazione, è facilmente intuibile: se si deve trattare un liquame questo viene raccolto in vasche o in ampi contenitori di altezza limitata, ed esposto al calore, tramite vari metodi. Il più economico è quello di esposizione al sole tramite concentratori di solito costituiti da lenti curvate (lenti di Fresnel) ma esistono anche altri metodi per far evaporare l’ acqua. Molti impianti usano serpentine o griglie ad immersione che vengono scaldate. L’ essicazione deve avvenire in ambiente aperto per cui particolare attenzione bisogna prestare all’ evaporazione di liquami che possano contenere residui zootecnici o sostanze biologiche o fisiologiche (es, urine, o sangue). Quando l’ essicazione invece coinvolge solidi, specialmente fanghiglia o materiali porosi che trattengono l acqua, il processo avviene in appositi macchinari chiamati Dryers, generalmente a sezione circolare, ove viene fatto passare un getto di aria calda. L’ efficienza di questi metodi dipende dai tempi e dalla superficie di contatto tra aria e materiale umido, per cui l’ ideale è utilizzare dryers in cui l’ aria compia più passaggi o percorsi non lineari.
Qui sotto lo schema di un sistema di essicazione di fanghi tramite dryer, dalla carica fino al disposal o trasferimento a vendita di pellets:




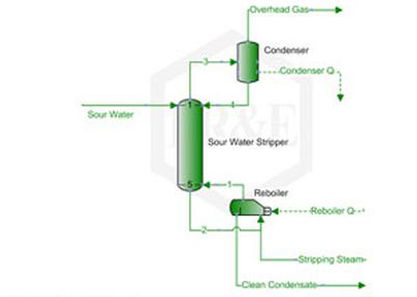
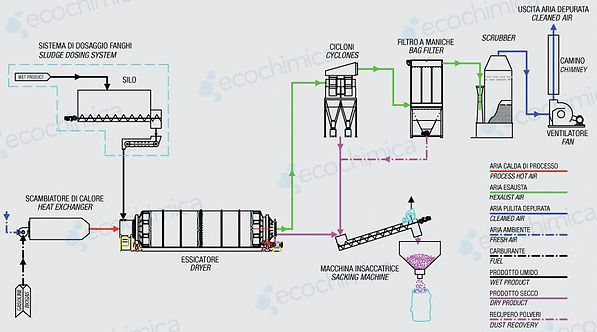