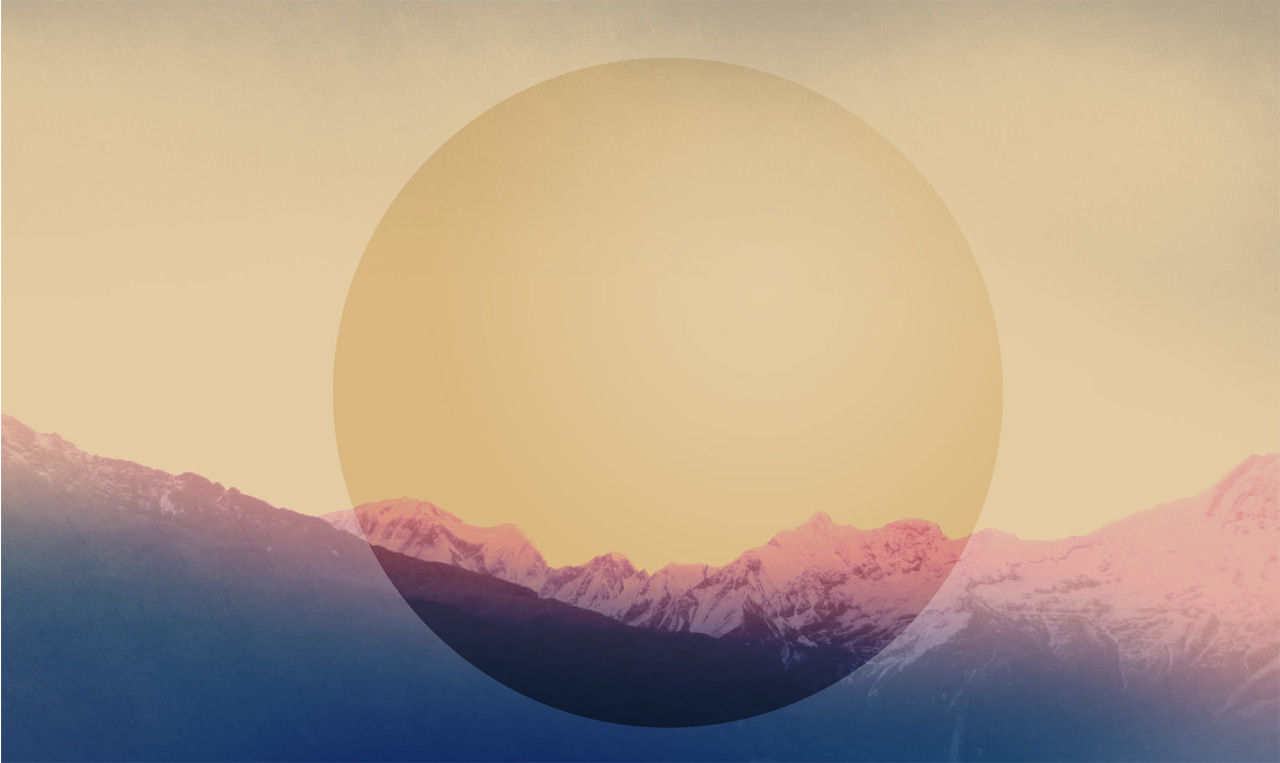
Seguici anche su:
Tecnologie Ambientali
Breve panoramica sul recupero dei metalli
Per il recupero di metalli si utilizzano tecnologie e impianti appositi che permettono una resa in recupero molto elevata. Il recupero di questi metalli è un passo importantissimo in quanto permette sia di risparmiare materie prime, sia di ridurre l’ impatto ambientale dovuto allo smaltimento, per esempio, degli elettrodomestici. Pensiamo per esempio ai famosi RAEE (rifiuti di apparecchiature elettriche ed elettroniche) contenenti Molibdeno, Tungsteno, Rame, Manganese, tutti metalli di valore che se recuperati possono essere riutilizzati per nuovi apparecchi elettronici (ma non solo) permettendoci di non dover comprare nuove materie prime. A parte questo, il recupero dei metalli dai RAEE, specie se di valore, è una risposta alle direttive comunitarie del 2002, 2003 e 2012.
Il recupero di questi metalli avviene sostanzialmente con tre processi:
-
Riduzione a liquido di metallo (definito ‘leaching’)
-
Filtrazione – separazione chimica, fisica o elettro-gravimetrica del risultato di leaching
-
Riduzione a pasta di metallo tramite altoforno o torcia al plasma
La tecnica di leaching è una riduzione a liquido che utilizza sostanze chimiche capaci di sciogliere (e quindi appunto di ‘ridurre a liquido’) le componenti metalliche, in parte o in toto, ottenendo una mistura liquida dalla quale poi per evaporazione, complessazione chimica o lavaggio chimico, si può recuperare il metallo desiderato.
Le tecniche di separazione chimica, fisica e elettro-gravimetrica si basano su processi quali lo scambio ionico, la separazione con solvente, il lavaggio chimico, la complessazione. In sostanza il mix liquido ottenuto tramite leaching viene sottoposto a processi di depurazione che sfruttano l’ affinità a questo o quell’ elemento chimico (estrazione con solvente, complessazione, separazione tramite scambio ionico e lavaggio chimico) o i principi di elettrolisi (elettrogravimetria) cioè la separazione di una fase metallica intorno a un elettrodo in base alla sua concentrazione.
Tra questi vari metodi il più utilizzato per resa, convenienza e semplicità di controllo, specialmente su grandi molti di liquido, è la separazione con solvente, o ‘estrazione liquido – liquido’ la quale sfrutta un processo mediante il quale una sostanza (nel nostro caso lo ione metallico) è trasferita da una fase liquida ad un'altra con essa immiscibile. Solitamente le due fasi sono rispettivamente acquosa e organica. Per realizzare questa operazione viene utilizzato un estraente, cioè una molecola avente proprietà complessanti che, reagendo secondo vari meccanismi con una sostanza disciolta nella fase acquosa, è in grado di estrarla. Di solito, per migliorare le proprietà chimico-fisiche dell'estraente, esso viene disciolto in un diluente che, in genere, non ha proprietà estrattive. Il diluente, insieme all'estraente, costituisce la cosiddetta fase organica.
La soluzione acquosa sottoposta all'estrazione di uno o più soluti costituisce il raffinato, mentre la fase organica caricata con il soluto dopo l'estrazione si chiama estratto.
La riduzione a pasta di metallo invece si ottiene sottoponendo i metalli ad altissima temperatura come avviene negli altoforno, né più né meno come si fa per ottenere la pasta di vetro. Questa massa fluida e densa rovente ha un basso grado di purezza e deve essere purificata.
Alternativamente si può utilizzare la tecnica della torcia al plasma, della quale abbiamo scritto abbondantemente su questo sito, la quale permette di avere un recupero di metallo puro e allo stesso tempo di generare una enorme quantità di energia.
Vedi anche: Distruzione dei rifiuti tramite torcia al plasma